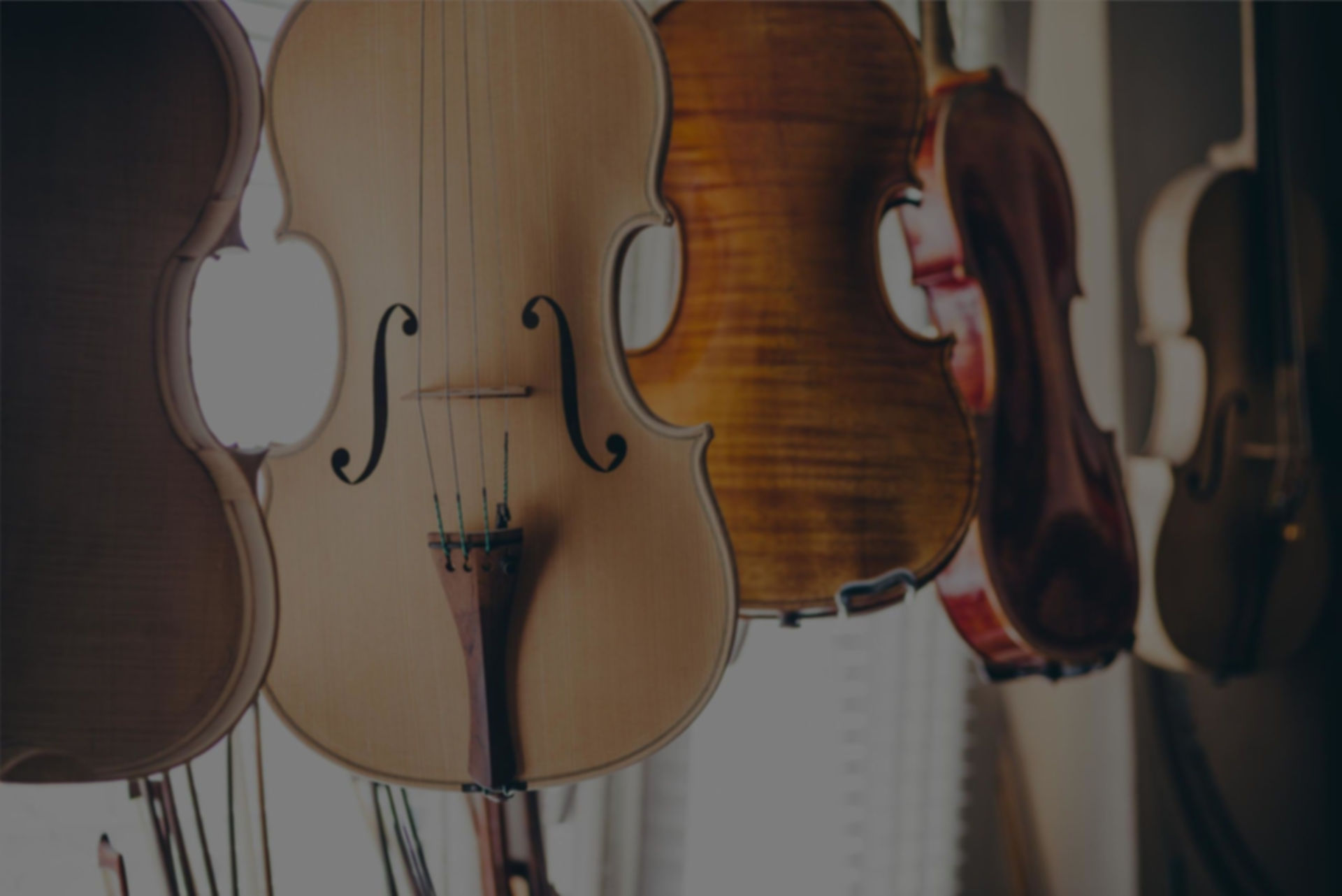

String Instrument Restoration and Bow Repairs
Whether your instrument has suffered only a small scratch to the varnish or catastrophic damage to the body, it is essential that the repair is done in a manner that respects both the integrity and the value of the instrument. Wherever possible, repairs should be reversible and the original wood and varnish preserved. At V.A. Hill Fine Strings Ltd., our team of Calgary luthiers uses recognized restoration techniques and traditional materials to repair damaged instruments. We realize that an improper repair can do more damage to a fine instrument than the original damage.
Our professionally trained luthier, Lianne Elkanah, handles all bow repairs and rehairs.
If you have any questions for our team, please get in touch.
The following are a few of the more common issues corrected by the luthiers at V.A. Hill Fine Strings Ltd.:
Open Seams
The glue used in violin making is designed to be reversible. This enables an instrument to be taken apart for repair. Because of this, the seams are prone to opening. While this can result in a change of sound or response, or even buzzing of the instrument, it is likely to save the plates from being cracked. Should you find an open seam, it is important that it be glued while the joint is still clean and that the gluing be done with tension removed from the strings. Never allow any repairer to use anything other than a reversible protein glue to repair a seam. "Uncle Charlie" may be able to repair it for free with the white glue from his workshop, but that could prove to be a very costly repair in the long run.
Improperly Shaped Fingerboards
With regular playing of the instrument, small dents are formed on the surface of the fingerboard by the action of the fingers on the strings. Over time, the surface of the fingerboard can become very uneven and when held to the light, looks much like a washboard road. This can cause the strings to rattle against the board and also make it difficult to play double stops in tune. The fingerboard should be evened out by removing the nut and resurfacing the board with a hand plane. This will eliminate the bumps and also produce the correct curvature. A properly shaped fingerboard is essential for correct intonation and the playing of effortless double stops.
Poorly Fitted Pegs
Pegs are affected by changes in humidity as well as by normal wear. In general, a regularly-used peg with an adequate lubricant will fit and hold for a longer period of time than a seldom-used, dried out peg. When an adjustment and the use of lubricant are no longer sufficient to hold a peg in tune, the peg needs to be refitted. This correction can be as simple as reshaping the pegs or as involved as re-bushing and re-drilling the entire set of peg holes and installing new pegs. When a peg becomes very hard to turn and "creaks" when it is forced to move, this peg is in jeopardy of being cracked or of cracking the peg box. This peg requires lubrication with a peg paste or attention from a qualified luthier.
Worn or Chipped Varnish
Hand wear or an impact, such as a knock from the bow or hitting a music stand, can remove varnish and expose bare wood. The resulting bare wood should be retouched as soon as possible to prevent dirt and moisture from penetrating the wood itself. Some players find that they wear through the varnish on the shoulder of their instrument very quickly. This is normally caused by higher than normal acidity in the person's system. Players with red hair often fit into this group. Should your violin require repeated repair for worn varnish on the upper shoulder, a plastic shield to protect this area is advisable.
Cracks
Depending upon the position, length, and condition, a crack can be anything from a minor problem which can be repaired in minutes, to a major disaster that can result in weeks of restoration work. In general, cracks are easier to repair when they are fresh and the exposed wood has not become dirty or distorted out of shape. Where cracks have been badly glued in the past, either out of position or with inappropriate glue, most of the repair time (and costs) will be spent on undoing the old repair. A dirty crack embedded with previously-used old glue cannot be re-glued without first being properly cleaned. If the instrument has opened, or the position of the crack will allow for it, all cracks should be reinforced on the inside of the instrument with wooden cleats, or a piece of parchment or silk.
Sound Post Cracks
Sound post cracks can occur on the front or the back of the instrument. On the top plate, the downward pressure of the bridge and the upward pressure of the nearby sound post make this area of the top plate very vulnerable to damage. A sharp blow to the sound post area of the back plate can crack either the back plate, the top plate, or both. To repair a sound post crack, gluing alone will not suffice as the pressure from the post will continually re-open the crack. The reinforcing of this type of crack will require a patch made from matching wood embedded on the inside of the plate with sufficient depth to replace most of the cracked wood. This type of repair is commonly referred to as a sound post patch.
Bass Bar Cracks
As in the sound post area, the pressure of the bridge foot and the resistance of the bass bar cause tension that can result in a crack along the bar. When the area along the length of the bass bar meets with some force, the top plate can crack along where the bass bar is glued to the inside. The most common repair to this type of damage involves removing the bass bar, gluing and cleating the crack and fitting a new bass bar to the repaired area. Often, the new bass bar will have to be fit over top of the cleats reinforcing the crack. The time required for this precise work often results in additional repair costs.
Damaged Buttons
The string tension puts a lot of strain on the neck. Much of this stress is stabilized by the button, which is part of the back plate. A severe blow to the instrument can result in the neck being forced out of the top block and breaking off the button, which remains glued to the base of the neck. Simply gluing the neck and button back into position is insufficient; the strength from the back plate is not restored as the button remains broken. New wood needs to be added from the inside to reinforce the area and give it extra strength from the plate to the underside of the neck. If the button is also damaged on the outside, or missing, it may also need to be replaced as a whole button graft. The outer edges of the button are sometimes fitted with an ebony cap to camouflage the damage in this area.
Worn or Damaged Bows
Bow maintenance is very important to your quality of sound. Bows should typically be rehaired every 12 to 18 months with normal use, and more frequently with heavier use. Indications that your bow needs a rehair are as follows:
There are too few hairs left in the bow
Rosin no longer remains on the hair but is caked onto the strings or coated on the top of the instrument
The hair is brittle and easily broken
The hair has absorbed oils from being handled and is visibly dirty
Our rehairs are offered in 2 grades of hair: premium, and black. For those who are more adventurous, we offer coloured rehairs in yellow, dark orange, green, purple, and blue. All rehairs and bow repairs are performed by our own professional bow maker.
Live Outside the Calgary Area?
If you live out of town, you can have your bow delivered to us for rehair or repair.
Should you not own a standard bow case, plastic PVC vacuum tubing or plumbing pipe cut to size make for great shipping containers. Wrap your bow in cloth or paper to prevent shock damage and ship it by mail or courier. If it is an expensive bow, be sure to consider the insurance. We will return your bow in the same carton and manner of delivery in which it was received.
Once we receive your bow, we will phone you to confirm the repairs and the cost. We will also ask for a credit card number at this time.
When the work is completed, we will charge the repair to your credit card and ship your bow back to you with all receipts.
For rehairs and minor repairs, the turn-around time is typically less than 7 days from the date of receipt. Major restorations may take longer, but we will discuss this with you prior to starting the repair.
All repairs and bow rehairs are performed to professional standards.
If you have any questions for our team, please get in touch.